X
Contact Us
+27 83 271 1808
+ 27 83 276 7922
+ 27 83 276 7922
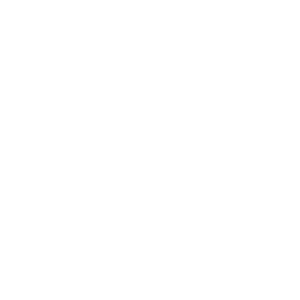
FOLLOW US
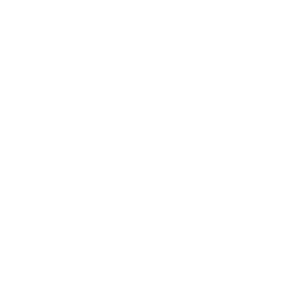
Call US
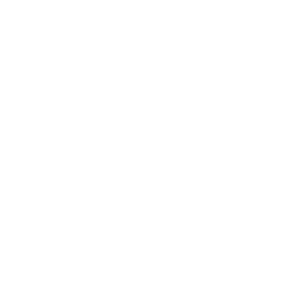
FOLLOW US
After separating the viscous mixtures (sludge and pastes) into solids and liquid. The solid fraction, still in viscous form, can then be valorized by drying it with the progressive pulse combustion drying (PCD) technology. If a waste stream, by-product or product can still be pumped there is a high probability that it can be dried by PCD, making it the most suitable anchor technology in the valorization process.
The term pulse combustion originates from the intermittent (pulse) combustion of gaseous fuel in the pulse combustion engine, in contrast to continuous combustion in conventional burners.
Such periodic combustions generate intensive pressure, velocity, and to a certain extent, temperature waves propagating from the pulse combustion unit through a tailpipe (a diffuser) to the process volume of the drying chamber.