X
Contact Us
+27 83 271 1808
+ 27 83 276 7922
+ 27 83 276 7922
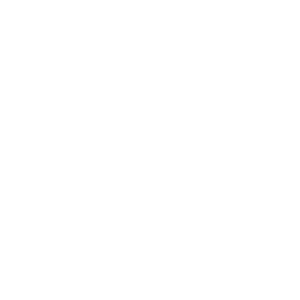
FOLLOW US
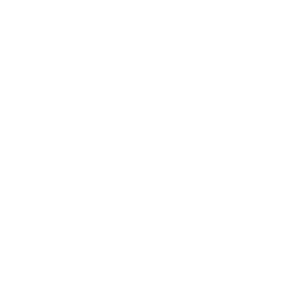
Call US
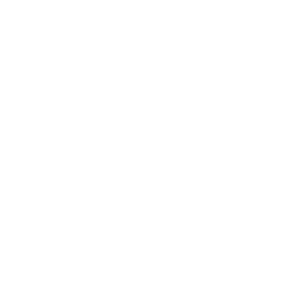
FOLLOW US
The first step in the valorizing process of products, by-products and waste streams in the form of viscous mixtures (sludge or slurry) is the dewatering of the viscous mixtures, separating the mixture into solids and liquid.
With regards to the dewatering of various types of sludge, Sinowatek presents the Fournier Rotary PressTM dewatering technology from Fournier Industries in Canada as the most advanced technology available.
The principle behind the Fournier Rotary PressTM is straightforward. Sludge is fed into a channel at low pressure that rotates between two parallel slow revolving (0.2 to 2 rpm) stainless steel filtering elements (screens).
As free water passes through screens, the sludge continues to dewater as it travels around the channel. The flocculated sludge builds up solids until enough pressure is generated against the outlet restrictor arm. The frictional force of the slow-moving filtering elements, coupled with controlled outlet restriction, generates enough back pressure to dewater the remaining solids, resulting in the extrusion of a very dry cake.
A single-width channel can dewater all varieties of sludge produced in industries like paper and pulp mills, factories, municipalities, breweries, bio-gasification, farming (animal manure), agro-food, and mining, without any physical modification.
Another outstanding feature of the Fournier Rotary PressTM is that units can be made expandable for increased capacity at a future date. Customers benefit from lower capital costs at purchase, with the ability to expand according to growing needs.
Any number of channel configurations can be provided, up to a maximum of 8 channels per press.
The Fournier Rotary PressTM is rapidly gaining ground in the rest of the world, replacing centrifuges, belt -, screw - and filter presses, for the following reasons: