X
Contact Us
+27 83 271 1808
+ 27 83 276 7922
+ 27 83 276 7922
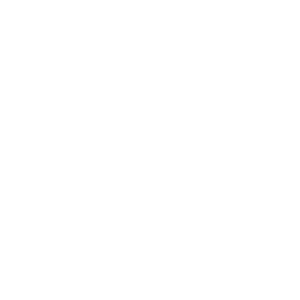
FOLLOW US
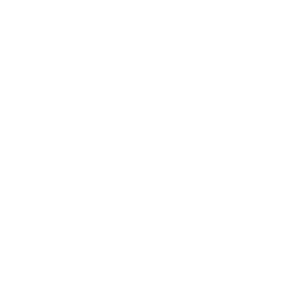
Call US
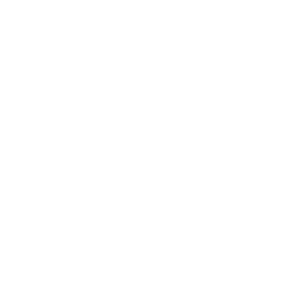
FOLLOW US
Every year, a staggering 1.6 billion tons of food, equating to one-third of the global food production, is lost or wasted. Meanwhile, nearly 10% of the world's population goes hungry. This mismanagement of resources has evolved into a pressing global dilemma, prompting the United Nations' Sustainable Development Goals, which aim to halve food loss and waste by 2030.
Transitioning the food and beverage system to one founded on the principles of the circular economy emerges as a potent strategy in combatting this issue.
The food system can undergo a profound transformation by reestablishing connections between communities and local food production. This shift entails reimagining the way we cultivate food, design food products, and manage by-products and waste.
Sinowatek plays a pivotal role in this transformation by leveraging innovative Pulse Combustion Drying (PCD) technology to convert food products, by-products, and waste streams into powders. Remarkably, this process preserves the core quality attributes of these products.
By adopting such a approach, businesses can not only reduce food waste but also unlock the potential for creating new, value-added products, thus closing the loop in the circular economy.
Milk is a fast perishable product and it is therefore important to preserve it for later consumption by drying it into powder. The solubility of the powder into water affects the reconstitution of the milk. Milk protein denaturation and/or aggregation during the drying process can alter the biological, chemical, and physical properties of the milk protein by mild disruption of its molecular structure and are therefore the main reason for reduced milk powder solubility.
Spray drying is a common method in milk powder production. In comparison with spray drying, the pulse combustion drying technology deliver powders with lower protein denaturation ensuring higher quality of the dried powder.
Sinowatek has a small commercial dryer available at the PCD Test Centre to test milk products to achieve the best dried product characteristics and to determine the operating parameters for industrial application.
Whey is produced in large volumes as a liquid by-product of the cheese making process. Whey contains proteins which can supply all the essential amino acids to the body while this perceived waste has a very high potential to be transformed into a profitable value-added product.
Sinowatek offers the advanced pulse combustion drying technology as an alternative to the well-established spray drying technology to transform the by-product into a high-quality food grade powder.
The PCD technology is environmentally friendly, with a high energy and thermal efficiency. The lower pressure required for mixture delivery and smaller equipment footprint also add to the cost effectiveness of the process.
Dried soybeans are ground and mixed with a solvent to prepare an extract for when spray drying is used to dry the extract. A fat removal stage is required during the preparation of the soybean extract. Drying carriers, such as maltodextrin and starch, generally are also added to the extract to improve the spray dryer performance.
Sinowatek dried soybean extract (a slurry) for a client in the small commercial pulse combustion dryer at the PCD Test Centre where the soybean extract slurry was delivered directly to the drying chamber through a single pipe injector (no nozzle etc.) where it was atomized delivering a powder product. No pre-processing or carriers are necessary for this drying technology.
The pulse combustion dryer delivered a powder superior to the spray drying power in terms of purity, flavour, texture, protein viability, colour, flowability and particle surface characteristics.
The smaller air volumes, lower pressure required for mixture delivery, reduced pre-treatment steps and smaller equipment footprint make the process more cost-effective than spray drying.
Insect meal protein (fly larvae) is becoming more economically feasible in South Africa and it is cost competitive to fishmeal. The inclusion of fly larvae powder in aquafeed is expected to have the greatest economic impact.
Part of the processing is the drying of the fly larvae slurry mixture and the pulse combustion drying technology is very suited for this process as seen by the drying of fly larvae slurry into powder at Sinowatek’s PCD Test Centre.
Due to the nutritional value of fruit and vegetables they are consumed raw, minimally processed, as well as fully processed. Significant losses and waste in the fresh and processing operations are becoming a serious nutritional, economical, and environmental problem.
The processing operations of fruits and vegetables produce wastes which consist mainly of seed, skin, rind, and pomace. These wastes contain good sources of potentially valuable bioactive compounds and can therefore be utilized in many different industries.
Fruits and vegetables are commonly produced seasonally and overproduction during the season and without proper utilization leads to waste of a significant portion of the fresh produce.
By converting these fruit and vegetable fresh produce and process specific wastes into powder ensure preservation and consequently new value-added products in other industries.
The pulse combustion drying technology is suited for the drying of fruit and vegetable products and wastes. First, the product must be converted into a slurry or paste through a pre-process (milling or grinding) to be fed to the drying chamber via a simple injector.
One of the biggest advantages of commercial drying with pulse combustion dryer is the ability to accommodate a variety of seasonal agricultural products in the same dryer throughout the year. This ensures an economical viable plant with a possibility of valorized output products the whole year round.
Sinowatek has a small commercial dryer available at the PCD Test Centre to test fruit and vegetable products and their processing wastes to achieve the best-dried product characteristics and to determine the commercial parameters for industrial application.
Spices and herbs are highly valued for their taste, aroma, colour, medicinal worth, and preservative action. Freshly harvested spices and herbs contain a high amount of moisture and numerous microorganisms.
Drying as a preservation method, immediately carried out after harvesting, prevent biological deterioration.
The drying method used should be executed carefully to retain flavour, aroma, colour, appearance, and nutritional value of the plants as much as possible. It is for this reason that Sinowatek offers the pulse combustion drying technology as an alternative to existing drying methods.
When drying plants and seeds with a PC dryer to deliver herbs and spices, the major quality parameters as indicated above are much better preserved than by most other technologies. The short residence time in the PC dryer limits the exposure of the product to heat and the effectively lower product temperature achieves high quality powder characteristics.
We offer to examine any herb and spice extract to determine if it can be dried by PCD. We ensure to achieve the best-dried product characteristics of the final product.
Living marine resources are limited; therefore, utilizing them sustainably is essential. Not all resources obtained from the sea are used adequately causing discards such as on-board waste with by-products and waste on land.
Fish-processing operations generate waste and by-products from inedible fish parts and endoskeleton shell parts from the crustacean-peeling process, particles of flesh, skin, scales, bones, visceral mass, head, fins, shells or liquid stick water. It has been estimated that about two-thirds of the total fish mass is discarded as waste and thereby creating enormous economic and environmental concerns.
By turning all these wastes into a pumpable slurry for preparation to dry it with pulse combustion drying technology through which it is turned into a high value powder for it to enter the circular economy loop.
We want to understand your specific challenges and problems. Please call us for an assessment or consultation.
1. Brewer’s spent yeast (BSY) drying
Milk is a fast perishable product and it is therefore important to preserve it for later consumption by drying it into powder. The solubility of the powder into water affects the reconstitution of the milk. Milk protein denaturation and/or aggregation during the drying process can alter the biological, chemical, and physical properties of the milk protein by mild disruption of its molecular structure and are therefore the main reason for reduced milk powder solubility.
Spray drying is a common method in milk powder production. In comparison with spray drying, the pulse combustion drying technology deliver powders with lower protein denaturation ensuring higher quality of the dried powder.
Sinowatek has a small commercial dryer available at the PCD Test Centre to test milk products to achieve the best dried product characteristics and to determine the operating parameters for industrial application.
Whey is produced in large volumes as a liquid by-product of the cheese making process. Whey contains proteins which can supply all the essential amino acids to the body while this perceived waste has a very high potential to be transformed into a profitable value-added product.
Sinowatek offers the advanced pulse combustion drying technology as an alternative to the well-established spray drying technology to transform the by-product into a high-quality food grade powder.
The PCD technology is environmentally friendly, with a high energy and thermal efficiency. The lower pressure required for mixture delivery and smaller equipment footprint also add to the cost effectiveness of the process.
2. Brewer’s spent grain
Brewer’s spent grain is most often sold as animal feed due to its properties and content of essential nitrogen-containing nutrients. The high moisture content (80%-90%) of this process waste makes it susceptible to microbial growth in the usual environmental conditions prevailing on farms. Within a few days after production, wet grain can undergo molding and spoiling. Therefore, dewatering and treatment for mold prevention are key factors in the utilization of this process waste.
Sinowatek offers the Fournier Rotary PressTM dewatering technology for reducing the moisture content from the spent grain slurry. The rotary press produces a high level of cake dryness and competitive production rates.
3. Spent Kieselguhr slurry
Kieselguhr (Diatomaceous Earth) is a chalk-like sedimentary mineral derived from fossilized shell-like remains of marine algae called diatoms. The shells are extremely fine and generally range in length from 40 to 160 μm and in width from 2 to 5 μm, the latter being roughly the diameter of most yeast cells. Because of their microscopic size and porous nature, Kieselguhr has been used extensively in the brewing industry as a filtering medium.
Due to the retention of organic material, especially yeast, proteins, and polyphenols by the end of the filtration, cake mass can be increased three times or more. Kieselguhr is a single-use product before being discarded due to its saturation.
The used kieselguhr is a slurry with a water content of 80-90 % creating a process waste that requires environmentally conscience disposal or recycling.
Discarded kieselguhr is stored in a tank capable of keeping the slurry (TS around 3%) in suspension before being routed through a Fournier Rotary PressTM where it is dewatered to a cake dryness of 35% TS, ready for disposal or recycling.
4. Bottle washing and filling plant
Filling is the last step of the beer brewing process and the first step of the packaging. Sanitary conditions at this stage have a direct impact on the shelf life of bottled beer.
The beer producers endeavour to deliver pure, fresh, tasty, and natural beverages with a long minimum shelf life with no preservatives or additional thermal treatment. Other marketing challenges are the variety of containment materials (glassware, PET, tinplate/aluminium, or the inside coated cardboard boxes) and long distribution paths.
Industrial sanitation (washing and disinfection) of the whole filling line is therefore a top priority in the industrial hygiene of beverage production.
With the conventional cleaning operating technology, the filler is emptied and flushed, disinfected, flushed again and afterwards re-filled. The complete cleaning procedure is therefore very time-consuming, cost-intensive and reduces the plant productivity.
An assortment of chemicals is used for aseptic filling or traditional custom filling. These chemicals cause high wear and corrosion of the filling equipment.
Sinowatek offers the INNOWATECH Anolyte® for the disinfection of filler equipment e.g. rinser, filler, bottle washer etc. INNOWATECH Anolyte® tradename SulafectTM is produced electrolytically from a high pure aqueous salt solution on-site with the Aquadron® system.
The disinfectant differs in its physical properties (colour, specific weight, density, viscosity, melting and freezing point) not much from pure water, as it contains only a low concentration of free chlorine. INNOWATECH Anolyte® tradename SulafectTM is a pH neutral, bactericidal, virucidal and fungicidal solution. Because of its low application concentration, it is odourless and tasteless, and, unlike traditional chlorine or chlorine dioxide disinfectants, it is gentle on materials it comes into contact with.
SulafectTM operates at lower concentrations but achieves higher germ-killing rates than conventional disinfectants. It effectively kills legionella, pseudomonads, and other germs, which can be especially prevalent in natural drink products. In addition, while preventing the formation of new ones.
With the bottle shower and SulafectTM system, disinfection of the filler table and surrounding areas is performed continuously. Thus, interruptions of production for in-between cleanings and disinfection can be avoided. The productivity of the plant increases, and water consumption is reduced.
The Aquadron® systems and the active agent Anolyte® (SulafectTM) have already proven reliable in the beer brewing industry for years.
Main advantages of using SulafectTM as a disinfectant:
Main advantages of using the Aquadron® system:
5. CIP system water treatment
In the brewing industry, impeccable hygiene is an essential precondition for making final products of consistently high quality and a long shelf life. A highly efficient CIP process in beer breweries is therefore non-negotiable.
The cleaning and disinfectant agents in conventional CIP stations are expensive and the CIP process requires a lot of time and effort. Materials are subject to rigid safety regulations for storage, handling, and disposal.
These agents kill germs aggressively while impacting the life of pipes and valves. Proactive thermal disinfection, as an alternative to chemicals, is also time-consuming and not always effective.
Sinowatek offers the INNOWATECH Anolyte® for the CIP system of a brewery. INNOWATECH Anolyte® tradename SulafectTM is produced electrolytically from a high pure aqueous salt solution on-site with the Aquadron® system.
The disinfectant differs in its physical properties (colour, specific weight, density, viscosity, melting and freezing point) not much from pure water, as it contains a very low concentration of free chlorine. INNOWATECH Anolyte® tradename SulafectTM is pH neutral, bactericidal, virucidal and fungicidal. Because of its low application concentration, it is odourless and tasteless, and, unlike traditional chlorine or chlorine dioxide disinfectants, it is gentle on materials it comes in contact with.
Although SulafectTM operates at lower concentrations it achieves higher germ-killing rates than conventional disinfectants. It effectively kills legionella, pseudomonads, and other germs, which can be especially prevalent in natural drink products.
Using the INNOWATECH Anolyte® (SulafectTM)system in the CIP plant gives rise to high disinfection activity. Individual programme steps such as acid treatment after the main cleaning step or fresh water rinsing after disinfection can be completely eliminated.
The Aquadron® systems and the active agent Anolyte® have already proven reliable in the beer brewing industry over an extended period.
Disinfection of CIP plants by INNOWATECH Anolyte® system replaces aggressive disinfection chemicals and saves water.