X
Contact Us
+27 83 271 1808
+ 27 83 276 7922
+ 27 83 276 7922
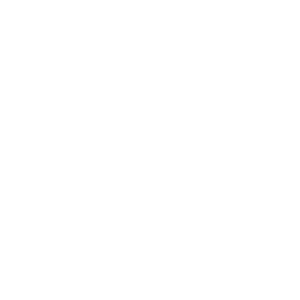
FOLLOW US
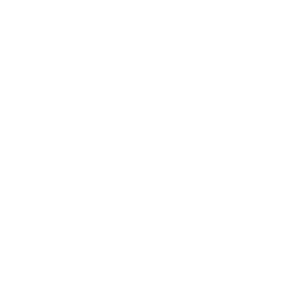
Call US
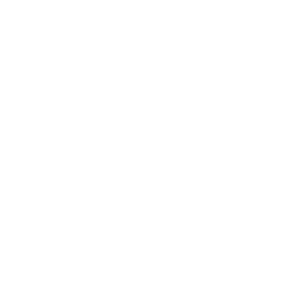
FOLLOW US
The Old WarOffice is a Grade II listed building with a rich and unique history. Completedin 1906, the building was once used by Prime Minister Winston Churchill andsits at the heart of Whitehall.
The 760,000 sq.ft. development brought the OWOback into use, creating a world class 5-star hotel and 85 apartments
The designers of the high-end renovated old building wanted to make sure that the water system stays in good shape for years to come, avoid lime scale and corrosion problems in the water related equipment and general piping system in the building.
In the summer of 2020, the contractors installed dozens of ¾” SB19-ET and 1” SB25-ET.ION ScaleBuster® water conditioners on all water inlet pipes for all apartments in the renovated building.
The solution offers great lime scale and corrosion prevention for all water systems in the building – protects all faucets, shower heads, toilet mechanisms, dishwashers and washing machines as well as the general piping systems of all apartments, with no energy use, no chemicals, no maintenance and with 10-yearmanufacturer’s warranty.
1. Brewer’s spent yeast (BSY) drying
The designers of the high-end renovated old building wanted to make sure that the water system stays in good shape for years to come, avoid lime scale and corrosion problems in the water related equipment and general piping system in the building.
2. Brewer’s spent grain
Brewer’s spent grain is most often sold as animal feed due to its properties and content of essential nitrogen-containing nutrients. The high moisture content (80%-90%) of this process waste makes it susceptible to microbial growth in the usual environmental conditions prevailing on farms. Within a few days after production, wet grain can undergo molding and spoiling. Therefore, dewatering and treatment for mold prevention are key factors in the utilization of this process waste.
Sinowatek offers the Fournier Rotary PressTM dewatering technology for reducing the moisture content from the spent grain slurry. The rotary press produces a high level of cake dryness and competitive production rates.
3. Spent Kieselguhr slurry
Kieselguhr (Diatomaceous Earth) is a chalk-like sedimentary mineral derived from fossilized shell-like remains of marine algae called diatoms. The shells are extremely fine and generally range in length from 40 to 160 μm and in width from 2 to 5 μm, the latter being roughly the diameter of most yeast cells. Because of their microscopic size and porous nature, Kieselguhr has been used extensively in the brewing industry as a filtering medium.
Due to the retention of organic material, especially yeast, proteins, and polyphenols by the end of the filtration, cake mass can be increased three times or more. Kieselguhr is a single-use product before being discarded due to its saturation.
The used kieselguhr is a slurry with a water content of 80-90 % creating a process waste that requires environmentally conscience disposal or recycling.
Discarded kieselguhr is stored in a tank capable of keeping the slurry (TS around 3%) in suspension before being routed through a Fournier Rotary PressTM where it is dewatered to a cake dryness of 35% TS, ready for disposal or recycling.
4. Bottle washing and filling plant
Filling is the last step of the beer brewing process and the first step of the packaging. Sanitary conditions at this stage have a direct impact on the shelf life of bottled beer.
The beer producers endeavour to deliver pure, fresh, tasty, and natural beverages with a long minimum shelf life with no preservatives or additional thermal treatment. Other marketing challenges are the variety of containment materials (glassware, PET, tinplate/aluminium, or the inside coated cardboard boxes) and long distribution paths.
Industrial sanitation (washing and disinfection) of the whole filling line is therefore a top priority in the industrial hygiene of beverage production.
With the conventional cleaning operating technology, the filler is emptied and flushed, disinfected, flushed again and afterwards re-filled. The complete cleaning procedure is therefore very time-consuming, cost-intensive and reduces the plant productivity.
An assortment of chemicals is used for aseptic filling or traditional custom filling. These chemicals cause high wear and corrosion of the filling equipment.
Sinowatek offers the INNOWATECH Anolyte® for the disinfection of filler equipment e.g. rinser, filler, bottle washer etc. INNOWATECH Anolyte® tradename SulafectTM is produced electrolytically from a high pure aqueous salt solution on-site with the Aquadron® system.
The disinfectant differs in its physical properties (colour, specific weight, density, viscosity, melting and freezing point) not much from pure water, as it contains only a low concentration of free chlorine. INNOWATECH Anolyte® tradename SulafectTM is a pH neutral, bactericidal, virucidal and fungicidal solution. Because of its low application concentration, it is odourless and tasteless, and, unlike traditional chlorine or chlorine dioxide disinfectants, it is gentle on materials it comes into contact with.
SulafectTM operates at lower concentrations but achieves higher germ-killing rates than conventional disinfectants. It effectively kills legionella, pseudomonads, and other germs, which can be especially prevalent in natural drink products. In addition, while preventing the formation of new ones.
With the bottle shower and SulafectTM system, disinfection of the filler table and surrounding areas is performed continuously. Thus, interruptions of production for in-between cleanings and disinfection can be avoided. The productivity of the plant increases, and water consumption is reduced.
The Aquadron® systems and the active agent Anolyte® (SulafectTM) have already proven reliable in the beer brewing industry for years.
Main advantages of using SulafectTM as a disinfectant:
Main advantages of using the Aquadron® system:
5. CIP system water treatment
In the brewing industry, impeccable hygiene is an essential precondition for making final products of consistently high quality and a long shelf life. A highly efficient CIP process in beer breweries is therefore non-negotiable.
The cleaning and disinfectant agents in conventional CIP stations are expensive and the CIP process requires a lot of time and effort. Materials are subject to rigid safety regulations for storage, handling, and disposal.
These agents kill germs aggressively while impacting the life of pipes and valves. Proactive thermal disinfection, as an alternative to chemicals, is also time-consuming and not always effective.
Sinowatek offers the INNOWATECH Anolyte® for the CIP system of a brewery. INNOWATECH Anolyte® tradename SulafectTM is produced electrolytically from a high pure aqueous salt solution on-site with the Aquadron® system.
The disinfectant differs in its physical properties (colour, specific weight, density, viscosity, melting and freezing point) not much from pure water, as it contains a very low concentration of free chlorine. INNOWATECH Anolyte® tradename SulafectTM is pH neutral, bactericidal, virucidal and fungicidal. Because of its low application concentration, it is odourless and tasteless, and, unlike traditional chlorine or chlorine dioxide disinfectants, it is gentle on materials it comes in contact with.
Although SulafectTM operates at lower concentrations it achieves higher germ-killing rates than conventional disinfectants. It effectively kills legionella, pseudomonads, and other germs, which can be especially prevalent in natural drink products.
Using the INNOWATECH Anolyte® (SulafectTM)system in the CIP plant gives rise to high disinfection activity. Individual programme steps such as acid treatment after the main cleaning step or fresh water rinsing after disinfection can be completely eliminated.
The Aquadron® systems and the active agent Anolyte® have already proven reliable in the beer brewing industry over an extended period.
Disinfection of CIP plants by INNOWATECH Anolyte® system replaces aggressive disinfection chemicals and saves water.