X
Contact Us
+27 83 271 1808
+ 27 83 276 7922
+ 27 83 276 7922
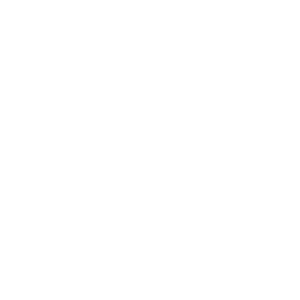
FOLLOW US
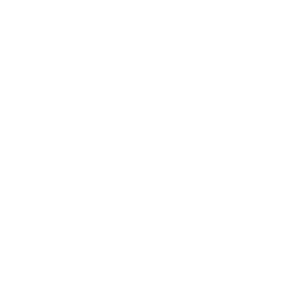
Call US
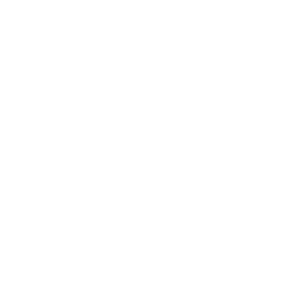
FOLLOW US
Yeast is a single-celled organism used in the manufacturing process of beer to convert sugars from grain to alcohol and carbon dioxide. Before full maturation of the beer, the excess yeast is collected and can be re-used up to six times in the brewing process. When the yeast is no longer useful it becomes Brewer’s spent yeast (BSY), the second biggest by-product of the brewing industry.
BSY can’t be disposed of into wastewater streams without pre-treatment because it has a very high chemical oxygen demand (COD) of 0.53kg/hl (1). A COD this high has detrimental effects on the environment and ecosystems that leads to a high waste stream cost.
However, BSY is high in nutrients, in particular proteins, vitamins, and minerals, therefore it can contribute to circular economies if processed correctly. To date, unfortunately, its industrial utilization has been limited due to the rapid contamination and spoilage because of the activity of micro-organisms. Drying BSY makes it last longer, but it can be an expensive process requiring large amounts of energy.
In the spirit of reaching sustainable goals and becoming more compliant with the circular economy concepts, breweries around the world are obligated to re-evaluate the drying technologies used in their plants due to the large amounts of energy required and associated high costs of the existing installed drying methods and equipment that currently produce the low value and low quality dried BSY co-product.
In the quest for a drying technology that is energy efficient and cost effective while ensuring a dried product of high value and quality, the new advanced Pulse Combustion Drying (PCD) technology aims to meet all these requirements.
Pulse combustion is a very old technology. The phenomenon of combustion-driven oscillations was first observed in 1777 and used in a variety of applications around the turn of the century but is now applied using modern materials and control.
The term pulse combustion originates from the intermittent (pulse) combustion of the gaseous fuel in the Pulse Combustion Engine that contrasts with continuous combustion in conventional burners. Such periodic combustions generate intense pressure, velocity, and to a certain extent, temperature waves that is propagated from the Pulse Combustion Unit through a tailpipe (a diffuser) to the process volume of the vertical Drying Chamber.
A low-pressure, slow-moving viscous feed of slurries or pastes is introduced through a singular pipe into the pulsating high velocity gas stream, at the top of the drying chamber.
As soon as the product stream meet the gas stream gas-dynamic atomization takes place. The initial droplets are quite large, because the feed introduction nozzle is a straight pipe with no restrictions. When the low-energy droplets experience the high energy of the gas stream, it breaks up into thousands of droplets through a process of successive division. The surface area of the droplets increases accordingly and efficient evaporation of the surface moisture (up to 98%) occurs. Atomization and evaporation happen at the same point in space and time, and under extremely turbulent conditions.
Within 3 to 6 milliseconds the pulsating exhaust gases with temperatures of 650°C-750°C produce ultra-fine (5-50μm) droplets and convert the surface moisture of the droplets into super-heated steam leaving behind a very dry fine powder with particles having a sphere shape and smooth surface.Even though the temperature of the gas used to dry the product is very high (650°C-750°C), sufficient energy is absorbed by the evaporating water allowing very little increase in the temperature of the solid particles themselves. This high evaporation rate coupled with the extremely short time the solids are exposed to the actual heat source, the characteristics of the solids are preserved.
A common environmental challenge with dryers is the formation of NOx gasses produced by boilers to provide energy for indirect dryers’ heat exchangers. The flame temperature is kept at an optimal temperature for efficiency, and this allows for the formation of NOx gasses. Despite the heat exchanger of the indirect drying system ensuring the dried product has no detectable NOx levels, the flue gas usually contains recordable levels of NOx (fuel and combustion temperature dependent).
In contrast, the flame temperature in the PCD burner is controlled to keep it well below 1300 °C to ensure that only negligible concentrations of NOx and other dioxins are formed. As a result, no significant levels of NOx or any dioxins are detected in the dried product and flue gas. This is especially advantageous in drying foods and bio-products destined for human consumption.
The energy efficiency of PCD is significantly (up to 50%) better than its nearest rival. When coupled with concentration processes and high solids content drying, PCD has definite advantages over traditional technologies.
The energy consumption of PCD dryers is 1.15 kW/kg water evaporated (thermal and electric). Studies indicated that the energy consumption of spray drying processes can be as high as 2.3 kW/kg (8.4 GJ/metric ton).
Pulse Combustion Dryers require less air than conventional dryers which results in smaller drying chambers and lower electrical consumption for smaller fans. Due to simple product injectors and smaller fans, running costs are 20-30% lower than spray driers.
The extremely short drying time indicates that the rates of heat and moisture transfer to and from the wet material are highly efficient, respectively. The advantage of this aspect of PCD ensures that sufficient energy is absorbed by the evaporating water allowing little increase in the temperature of the solids. This protects the quality attributes (nutritional value, color, taste, and aroma) of the solids better than all the other drying methods, except freeze drying. Freeze drying provides good quality powders but is more expensive in most powder drying applications.
The short residence time of powders in a PCD allows for faster material throughput.
The short residence time limits the exposure of product and the effectively lower product temperatures mean reduced denaturing of proteins and improves the level of available digestible protein. PCD also inactivates enzymes and harmful micro-organisms.
Overall, when drying food or by-products of processed food, the major quality parameters of the dried product such as natural color, flavor, retention of nutrients (proteins, fats, antioxidants, etc.), re-hydration properties and chemical stability are minimally affected by PCD.
Lower pressure required for mixture delivery
To effectively atomize viscous mixtures in a spray dryer, the mixture is delivered to the spray nozzles at high pressure (12 – 30 bar). In a PCD dryer the viscous mixture is delivered to the injector nozzle at 1 - 2 bar via a low-pressure pump. The result is that mixtures with higher TS content can be pumped through the delivery system.
When comparing drying units with the same powder production rate, it can be expected that the PCD dryer will occupy a significantly smaller floor area.
Pre-processing of the BSY is required to prepare it for efficient drying of a quality product. Pasteurization and dewatering are key steps of this process as the dewatering step substantially reduces the liquid to be evaporated by the PCD process.
The methods most commonly used to reduce the liquid portion and raise the total solids (TS) content are spinning typically in a decanter or through evaporative methods typically a multi effect evaporator.
It was found that the use of a decanter to process BSY has several drawbacks.
Evaporative dewatering methods are preferred
The high TS BSY is dried by the PCD, separated from the vapor and transferred to a storage hopper.
Dry BSY powder is bagged from the storage hopper and prepared for shipping as per the clients’ specification.
In conclusion, breweries with no drying equipment or existing installed spent yeast drying equipment that use large amounts of energy with associated high cost and that produce low value and low quality dried BSY co-product, may consider improving their situation by implementing the new innovative Pulse Combustion Drying (PCD) method and equipment. PCD technology is environmentally friendly, with a high energy and thermal efficiency. The lower pressure required for mixture delivery and smaller equipment footprint also add to the cost effectiveness of the process. The most attractive benefit of PCD is the profitable high quality food grade dried BSY that it delivers as the input to a circular bio-economy.
References
(1) Brewer’s Spent Yeast (BSY), an Underutilized Brewing By-Product - A Review
Alice Jaeger, Elke K. Arendt, Emanuele Zannini and Aylin W. Sahin,
Fermentation 11 December 2020